Vergärungsverfahren
Bei der Erzeugung von Biogas durch anaerobe Verfaulung können verschiedene Verfahrensvarianten unterschieden werden.
Verfahren zur Biogaserzeugung
- Einstufig
- Zweistufig
- Mehrstufig
- Diskontinuierlich
- Quasikontinuierlich
- Kontinuierlich
- Psychrophil
- Mesophil
- Thermophil
- Nassvergärung
- Trockenvergärung
Anzahl der Prozessstufen
Der Biogasprozess läuft in mehreren Phasen ab. Landwirtschaftliche Biogasanlagen werden größtenteils als ein- oder zweistufige Anlagen ausgeführt. Durch die Betriebsweise der Fermenter bzw. die Anordnung einer oder mehrer Fermenter kann dieser Stufenprozess mehr oder weniger gut nachgebildet werden. Die Systemauswahl hat Einfluss auf die Investitionskosten (Größe und Anzahl der Behälter), auf die Betriebskosten (Aufwand für Durchmischung) und Gasertrag.
Einstufige Anlage
Bei einer einstufigen Anlage werden die verschiedenen Prozessphasen (Hydrolyse, Versäuerung, Essigsäurebildung und Methanbildung) in einem Behälter durchlaufen.
Zweistufige Anlage/mehrstufige Anlage
Bei zwei- bzw. mehrstufigen Anlagen können die Phasen der Vergärung in verschiedenen Behältern ablaufen. Bei einer zweistufigen Anlage finden die Hydrolysephase und die Versäuerungsphase in getrennten Behältern statt. Dadurch können die Prozessbedingungen besser auf die Anforderungen der jeweiligen Phase abgestimmt werden.
Art der Beschickung
Diskontinuierliche Beschickung
Bei der diskontinuierlichen Beschickung wird der gesamte Fermenter in einem Schritt mit frischem Substrat gefüllt und luftdicht verschlossen. Das gesamte Substrat bleibt die gesamte Verweilzeit im Fermenter. Diese Art der Beschickung hat vor allem bei Trockenvergärungsanlagen Bedeutung.
Quasikontinuierliche und kontinuierliche Beschickung
Von quasikontinuierlicher Beschickung kann gesprochen werden, wenn mindestens einmal pro Tag Substrat in den Fermenter eingebracht wird. Durch eine Automatisierung des Einbringsystems ist es auch möglich, mehrmals täglich kleinere Mengen von Substrat in den Fermenter einzubringen. Diese kontinuierliche Beschickung hat sich als vorteilhaft erwiesen, da sich dadurch ein kontinuierlicher Gasertrag ergibt.
Die folgenden Anlagensysteme können mit quasikontinuierlicher oder kontinuierlicher Beschickung ausgeführt sein.
Speicheranlage
Der Fermenter und das Lager für die Gärreste sind in einem Behälter zusammengefasst. Beim Ausbringen des Gärrestes wird das gesamte ausgefaulte Substrat (bis auf einen Rest, der zum Animpfen des frischen Substrats verwendet wird) entnommen. Die Gasproduktion ist nicht so gleichmäßig wie bei einem Durchflussverfahren.
Abbildung 1: Speicheranlage
![Das Bild zeigt die schematische Darstellung einer Speicheranlage: Zulauf und Entnahme erfolgen im unteren Bereich des Gärbehälters, der gleichzeitig als Lager dient. Im oberen Bereich des geschlossen Gärbehälters sammelt sich das Biogas und wird abgeleitet.
[Weiland 2000]](/_internal/cimg!0/4g9xwjd9owtsuuaxi0btt8pxru69qb6.png)
![Das Bild zeigt die schematische Darstellung einer Speicheranlage: Zulauf und Entnahme erfolgen im unteren Bereich des Gärbehälters, der gleichzeitig als Lager dient. Im oberen Bereich des geschlossen Gärbehälters sammelt sich das Biogas und wird abgeleitet.
[Weiland 2000]](/_internal/cimg!0/axpn27nsxx08bnwkpihljhsyedzpjsi.png)
[Bildbeschreibung einblendenBildbeschreibung ausblenden]
Das Bild zeigt die schematische Darstellung einer Speicheranlage: Zulauf und Entnahme erfolgen im unteren Bereich des Gärbehälters, der gleichzeitig als Lager dient. Im oberen Bereich des geschlossen Gärbehälters sammelt sich das Biogas und wird abgeleitet. [Weiland 2000]
Durchflussanlage
Aus einer Vorgrube wird das Substrat mehrmals am Tag, im Idealfall kontinuierlich, in den Fermenter eingebracht. Gleichzeitig wird die gleiche Menge Substrat in den Gärrestbehälter gepumpt. Bei diesem Verfahren kann eine gleichmäßige Gasproduktion erreicht werden.
Abbildung 2: Durchflussanlage
![Das Bild zeigt die schematische Darstellung einer Durchflussanlage: Das Substrat wird im unteren Bereich des Gärbehälters eingebracht, gleichzeitig im oberen Teil entnommen und in den Lagerbehälter gepumpt. Im oberen Bereich des geschlossen Gärbehälters sammelt sich das Biogas und wird abgeleitet.
[Weiland 2000]](/_internal/cimg!0/eeosgqmuq1k1yt7rmtnn34j13bh1kpo.png)
![Das Bild zeigt die schematische Darstellung einer Durchflussanlage: Das Substrat wird im unteren Bereich des Gärbehälters eingebracht, gleichzeitig im oberen Teil entnommen und in den Lagerbehälter gepumpt. Im oberen Bereich des geschlossen Gärbehälters sammelt sich das Biogas und wird abgeleitet.
[Weiland 2000]](/_internal/cimg!0/jhxsxfxn996x3ykhnjm430a39xynda6.png)
[Bildbeschreibung einblendenBildbeschreibung ausblenden]
Das Bild zeigt die schematische Darstellung einer Durchflussanlage: Das Substrat wird im unteren Bereich des Gärbehälters eingebracht, gleichzeitig im oberen Teil entnommen und in den Lagerbehälter gepumpt. Im oberen Bereich des geschlossen Gärbehälters sammelt sich das Biogas und wird abgeleitet. [Weiland 2000]
Durchfluss-Speicher Anlage
Bei diesem Verfahren ist auch das Gärrestlager (Nachgärbehälter) abgedeckt. Dadurch kann das hier anfallende Biogas auch genutzt werden. Es wird eine gleichmäßige Gasproduktion erreicht.
Abbildung 3: Durchfluss-Speicheranlage
![Das Bild zeigt die schematische Darstellung einer Durchfluss-Speicheranlage: Ähnlich wie beider Durchflussanlage wird auch hier das Substrat im unteren Bereich des Gärbehälters eingebracht, gleichzeitig im oberen Teil entnommen und in den Lagerbehälter gepumpt. Beide Behälter sind geschlossen, das Biogas sammelt sich jeweils im oberen teil und wird abgeleitet.
[Weiland 2000]](/_internal/cimg!0/ir5b05y4gv2koh4jf8zcbinqfqyj6oz.png)
![Das Bild zeigt die schematische Darstellung einer Durchfluss-Speicheranlage: Ähnlich wie beider Durchflussanlage wird auch hier das Substrat im unteren Bereich des Gärbehälters eingebracht, gleichzeitig im oberen Teil entnommen und in den Lagerbehälter gepumpt. Beide Behälter sind geschlossen, das Biogas sammelt sich jeweils im oberen teil und wird abgeleitet.
[Weiland 2000]](/_internal/cimg!0/qy1at49d1bm4hxd6nles2mmvul5g8c2.png)
[Bildbeschreibung einblendenBildbeschreibung ausblenden]
Das Bild zeigt die schematische Darstellung einer Durchfluss-Speicheranlage: Ähnlich wie beider Durchflussanlage wird auch hier das Substrat im unteren Bereich des Gärbehälters eingebracht, gleichzeitig im oberen Teil entnommen und in den Lagerbehälter gepumpt. Beide Behälter sind geschlossen, das Biogas sammelt sich jeweils im oberen teil und wird abgeleitet. [Weiland 2000]
Prozesstemperatur
Bei der Biogasvergärung kann zwischen
-
psychrophilen (15-25°C),
-
mesophilen Anlagen (32- 38°C) und
-
hermophilen Anlagen (42 bis 55°C) unterschieden werden.
Landwirtschaftliche Anlagen arbeiten zum Großteil im Temperaturbereich zwischen 32 und 38°C. Thermophile Anlagen haben in der Regel eine höhere Biogasausbeute, der Vergärungsprozess ist aber im Vergleich zum mesophilen Bereich nicht so stabil und der Prozesswärmebedarf ist höher.
Eine thermophile Vergärung wird manchmal auch mit einer mesophilen Prozessstufe kombiniert.
Trockensubstanzgehalt
Abhängig vom Trockensubstanzgehalt im Fermenter kann zwischen Nassvergärung und Trockenvergärung unterschieden werden.
Nassvergärung
Die Nassvergärung ist das Standardverfahren bei der Erzeugung von Biogas, dabei wird pumpfähiges Substrat eingesetzt. Unterschieden wird in liegende und stehende Fermenter.
Liegende Fermenter
Diese haben eine zylindrische Form und werden oft als Stahltank ausgeführt. Diese Anlagen sind durch die Größe des Fermentervolumens (bis ca. 800 m³) beschränkt und werden daher entweder als Vorfermenter für größere Anlagen oder als Hauptfermenter für kleinere Anlagen eingesetzt. [FNR 2005]
Liegende Fermenter können nach dem Pfropfenstromverfahren arbeiten. Dabei wird der Verdrängungseffekt vom frischen Substrat ausgenützt um eine Strömung im liegenden Fermenter einzustellen. Bei diesem Verfahren kann die Aufenthaltszeit für das Substrat gut eingehalten werden, da es zu keinen Kurzschlussströmen kommt.
Stehender Fermenter
Diese Fermenterbauform wird am häufigsten ausgeführt. Es können Stahlbeton, Stahl oder Edelstahl als Material eingesetzt werden. Es ist ein Fermentervolumen bis zu 30.000 m³ möglich. Zur besseren Durchmischung werden die Fermenter meist nicht größer als 6000 m³ gebaut. [FNR 2005]
Das Volumen des Fermenters (m³) kann mit der täglich zugeführten Substratmenge und der angestrebten Verweilzeit abgeschätzt werden. Je länger die Verweilzeit desto höher ist die Gasausbeute.
Trockenvergärung
Bei der Trockenvergärung wird schüttfähiges Substrat eingesetzt. Die technische Entwicklung der am Markt angebotenen Verfahren zur Trockenvergärung ist aber noch nicht abgeschlossen. Die Raumbelastung ist durch den hohen Trockensubstanzgehalt sehr hoch, der Platzbedarf ist geringer und auch die Investitionskosten sind niedrig. Die Raumbelastung gibt an, welche Menge an organischer Trockensubstanz pro Kubikmeter Fermentervolumen zugeführt werden kann, ohne die Stabilität des Vergärungsprozess zu gefährden.
Probleme können sich bei der Ausgasung der nicht durchmischten Reaktoren ergeben. Außerdem besteht die Gefahr der Zonenbildung. In diesen Zonen kann der Wassergehalt zu hoch oder zu niedrig sein oder es können sich Versäuerungszonen ohne Methanproduktion ausbilden. [FNR 2005]
Die Trockenvergärung eignet sich für Betriebe, in denen keine Gülle als Basissubstrat anfällt. Um sich das Anmaischen mit hohem Energie- und Wasserbedarf zu ersparen kann eine Trockenvergärung sinnvoll sein.
Mischeinrichtung
Es können verschieden Durchmischungsverfahren unterschieden werden.
-
Mechanische Mischeinrichtung
- Tauchmotor-Propellerrührwerk
- Langachsrührwerk
- Axiale Rührwerk
- Paddel- oder Haspelrührwerk
-
Pneumatische Mischeinrichtung
-
Hydraulische Mischeinrichtung (Gaseinpressung)
Abgesehen von der Anordnung und der Betriebsweise der Fermenter bestehen auch noch verschiedene Systeme zur Durchmischung des Gärgutes. In der Praxis muss für die Mischung zwischen niedrigen Betriebskosten und einer optimalen Homogenisierung (z.B. zur Verhinderung von Schwimmdecken) abgewogen und ein Kompromiss gefunden werden.
Prinzipielle Mischungsvarianten sind in folgender Abbildung ersichtlich. Aufgrund der Erfahrungen der letzten Jahre haben sich vorwiegend mechanische Durchmischungssysteme durchgesetzt.
Abbildung 4: Systeme zur Durchmischung des Gärgutes, schematisch
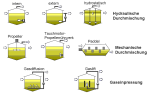
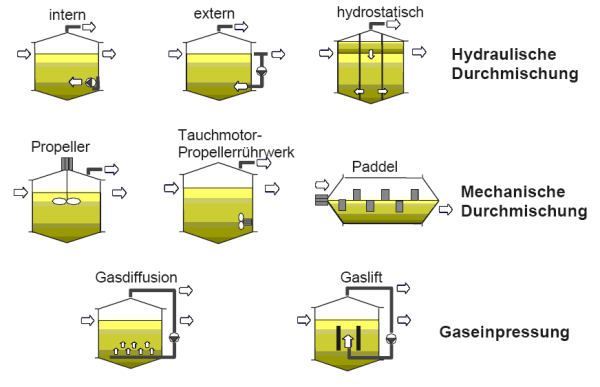
[Bildbeschreibung einblendenBildbeschreibung ausblenden]
Das Bild zeigt schematisch verschiedene Systeme zur Substratdurchmischung:
Im Bereich der hydraulischen Durchmischung kann das Gärgut entweder intern durch eine im Behälter angebrachte Pumpe umgewälzt werden oder es wird im oberen Bereich des Behälters entnommen und unten unter Druck wieder eingebracht. Eine dritte Möglichkeit besteht durch Ausnutzen der hydrostatischen Wirkung
Eine mechanische Durchmischung erfolgt entweder durch einen zentral im Gärbehälter angebrachten axialen Propeller, ein Tauchmotor-Propellerrührwerk an der Behälterwand oder ein Paddelrührwerk mit liegender Achse.
Bei der Gaseinpressung wird Gas aus dem oberen Teil des Behälters entnommen und in das Gärgut eingepresst. Diese Einpressung erfolgt bei der Gasdiffusion durch eine Vielzahl kleiner Düsen im unteren Bereich des Behälters, beim so genannten Gaslift wird das Gas zentral eingebracht. [Linke et.al. 2003]